
DELICATE DENSITY - R&D
Collaboration with Concrete Works
A concrete exploration using 3D printed molds with a goal to see how delicate, detailed, and finite concrete can get while still being structurally rigid. Ultimately the focus was to create a piece of furniture that embodies an optimal balance of delicateness in form and strength in dentistry. Using 3D printing as a new way to realize concrete through its ability to make molds, we have been interested in pushing the concrete’s natural limitations through fine geometries. It has become more common to use CNC technology and now 3D printing to realize repeatable one-of-a-kind forms that challenge what it can and cannot be done.
Our explorations are geared toward understanding the minimal threshold of form while still retaining its full inherent capacity of strength. Standard FDM prints create 23 pieces of PLA plastic molds that fasten together to create a large 5ft investment moldable to withstand up to 200 lbs of unreinforced Ultra-High-Performance Concrete. The order in which the pieces were assembled played a huge role in how well the pieces aggregated together. Even with absolute printing precision, the plastic can crack, warp and often create uneven surfaces that require a lot of post-process work to fully function as a watertight mold for concrete especially when put onto a vibration surface. Concrete was fed into 10 legs that start from 3 major openings and flow down.
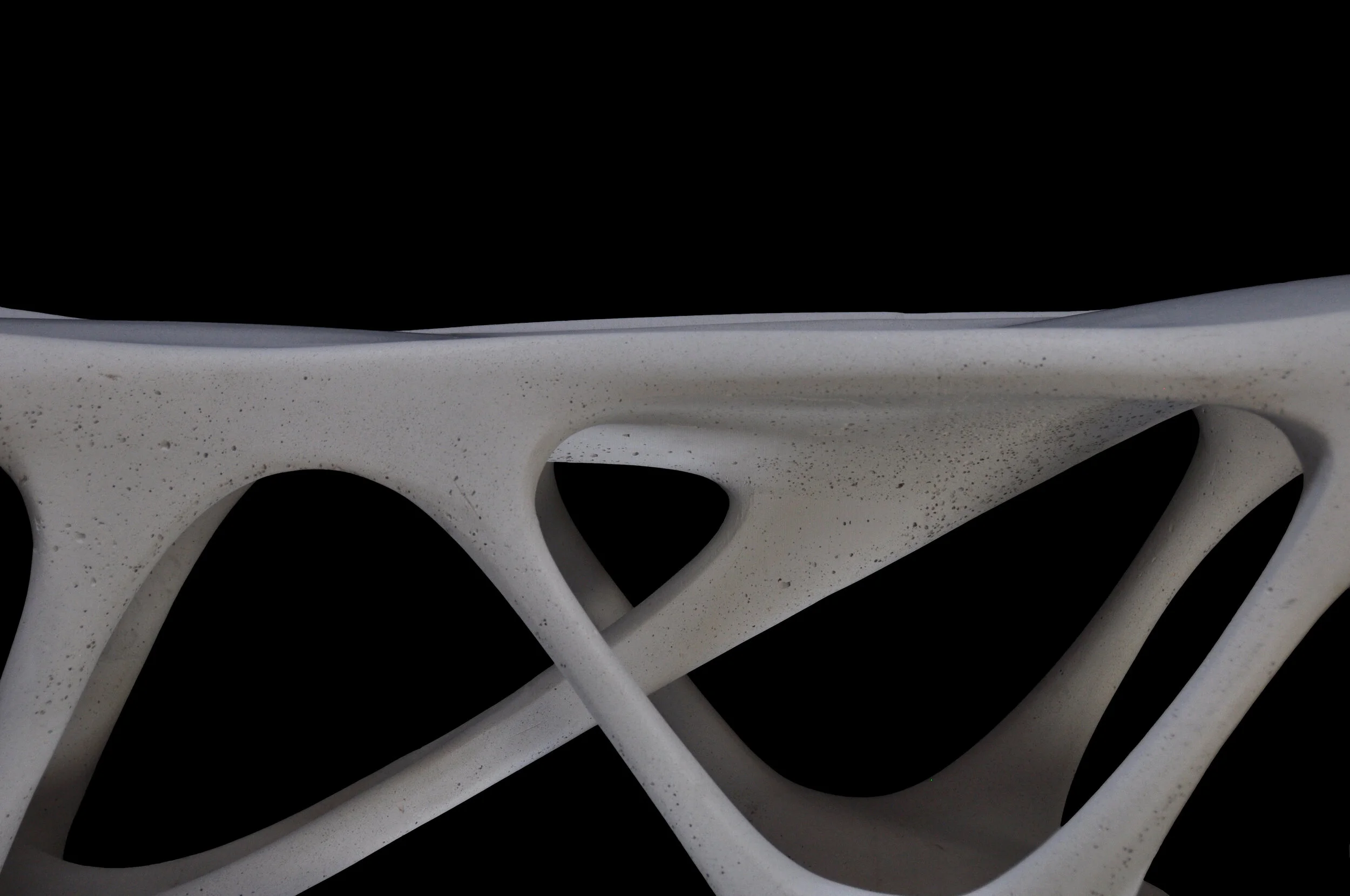
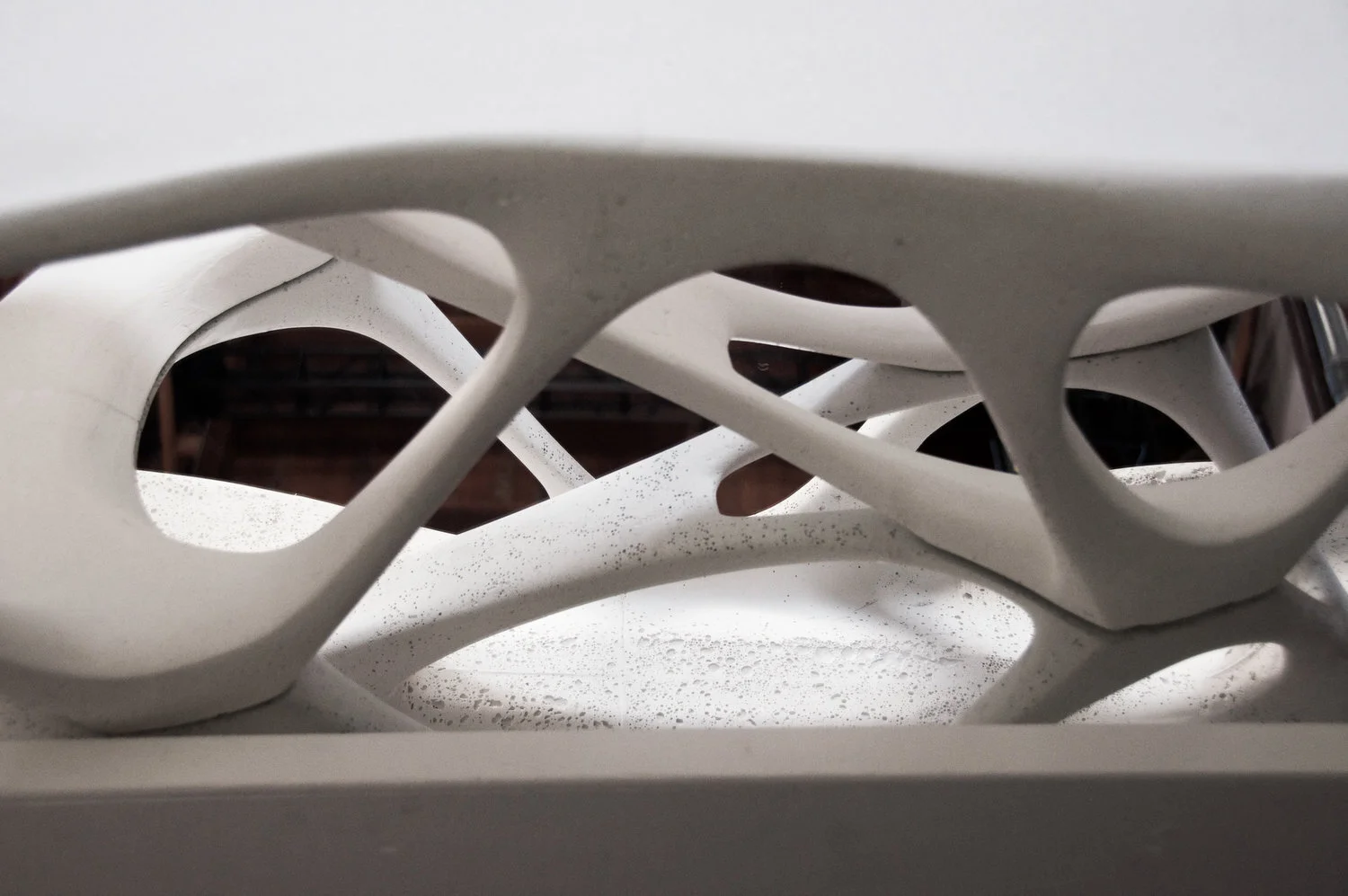
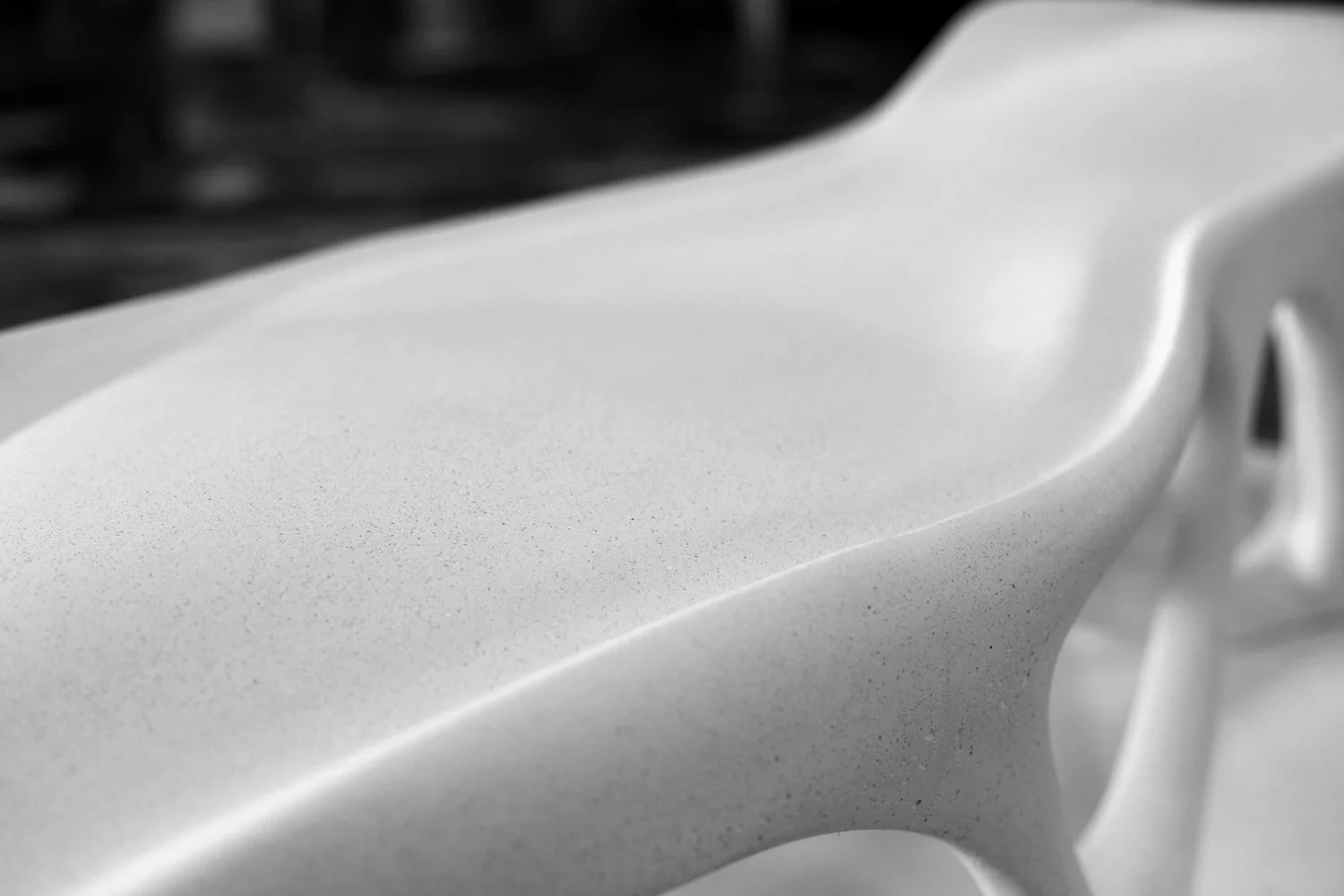
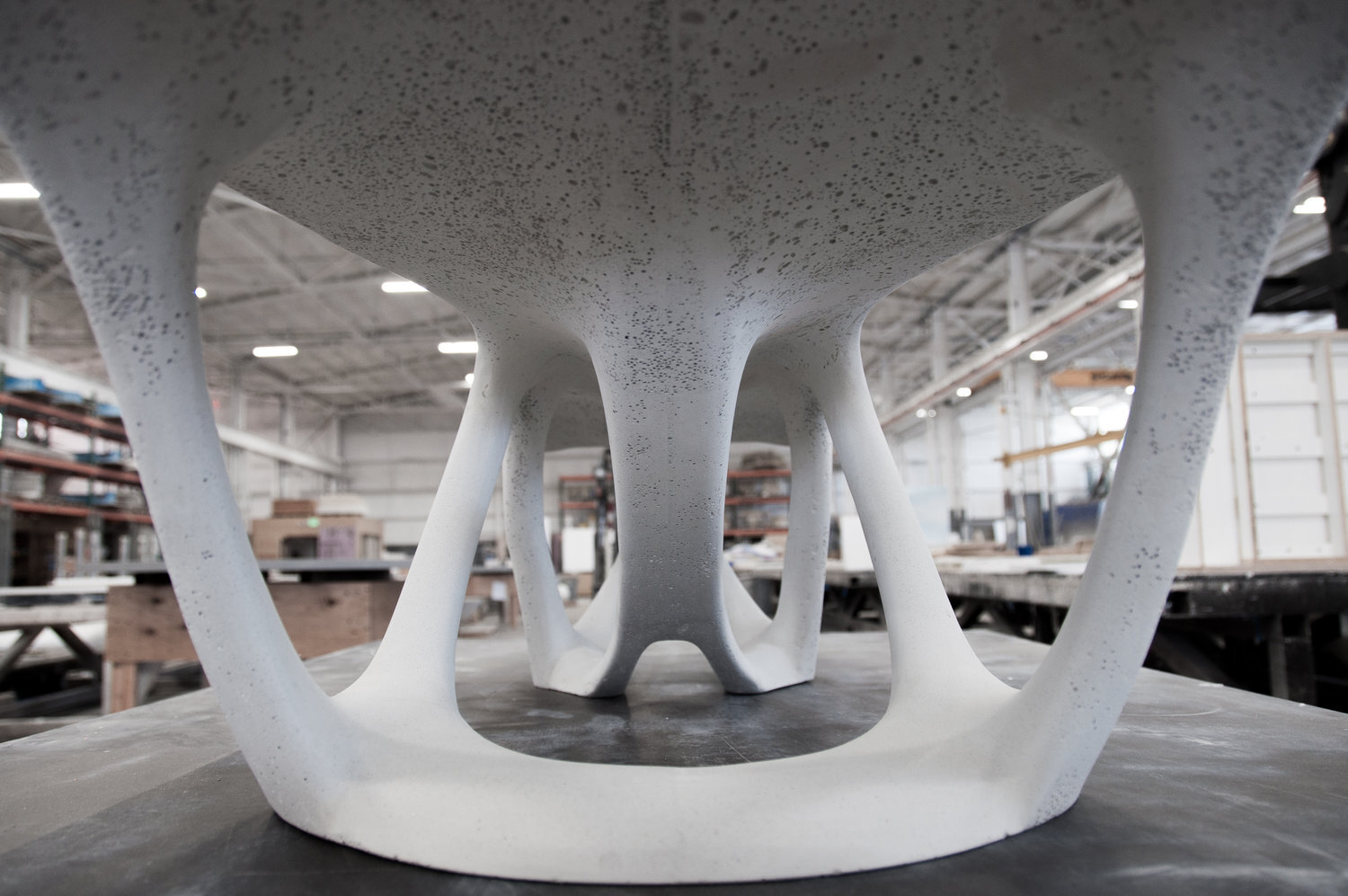
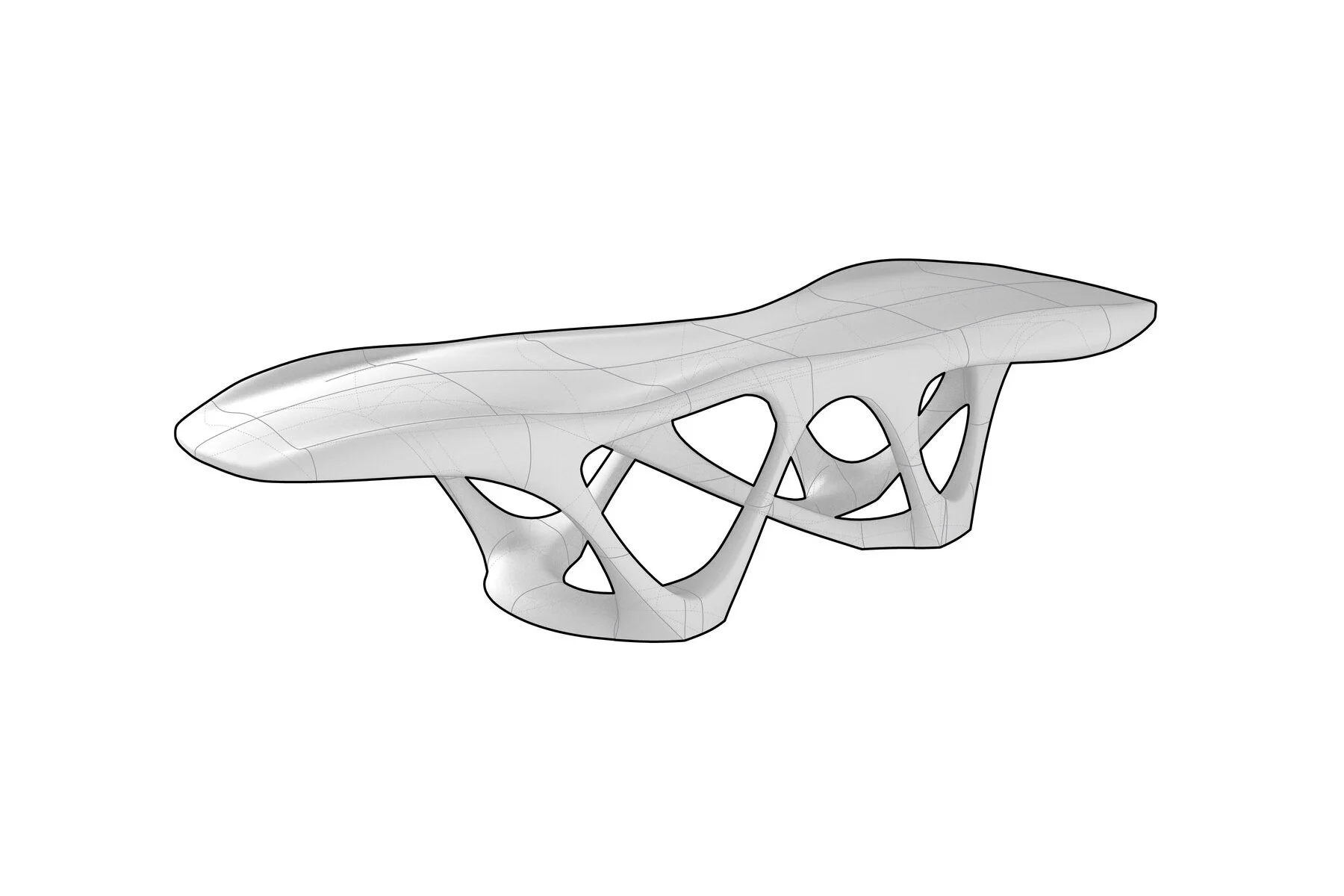
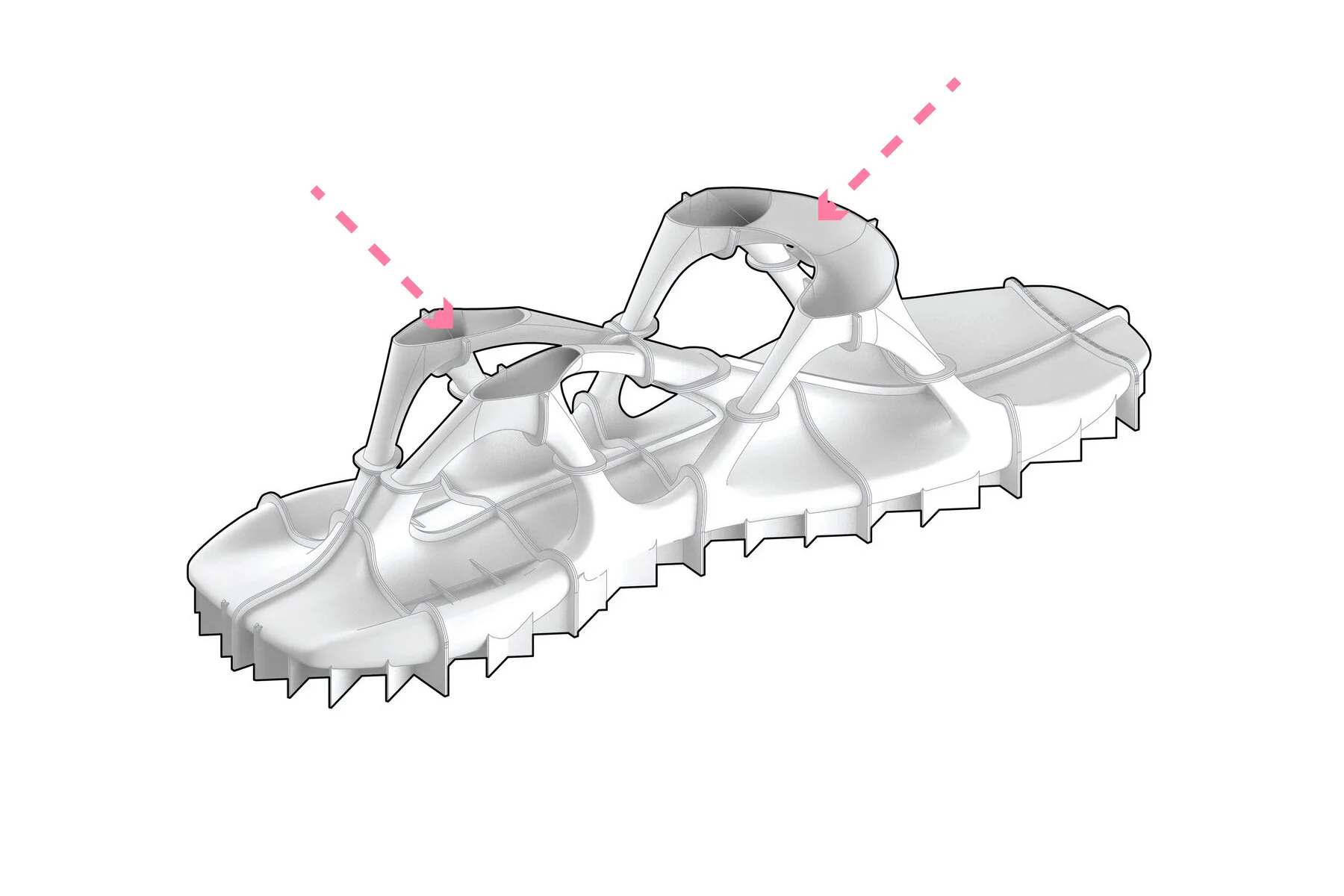
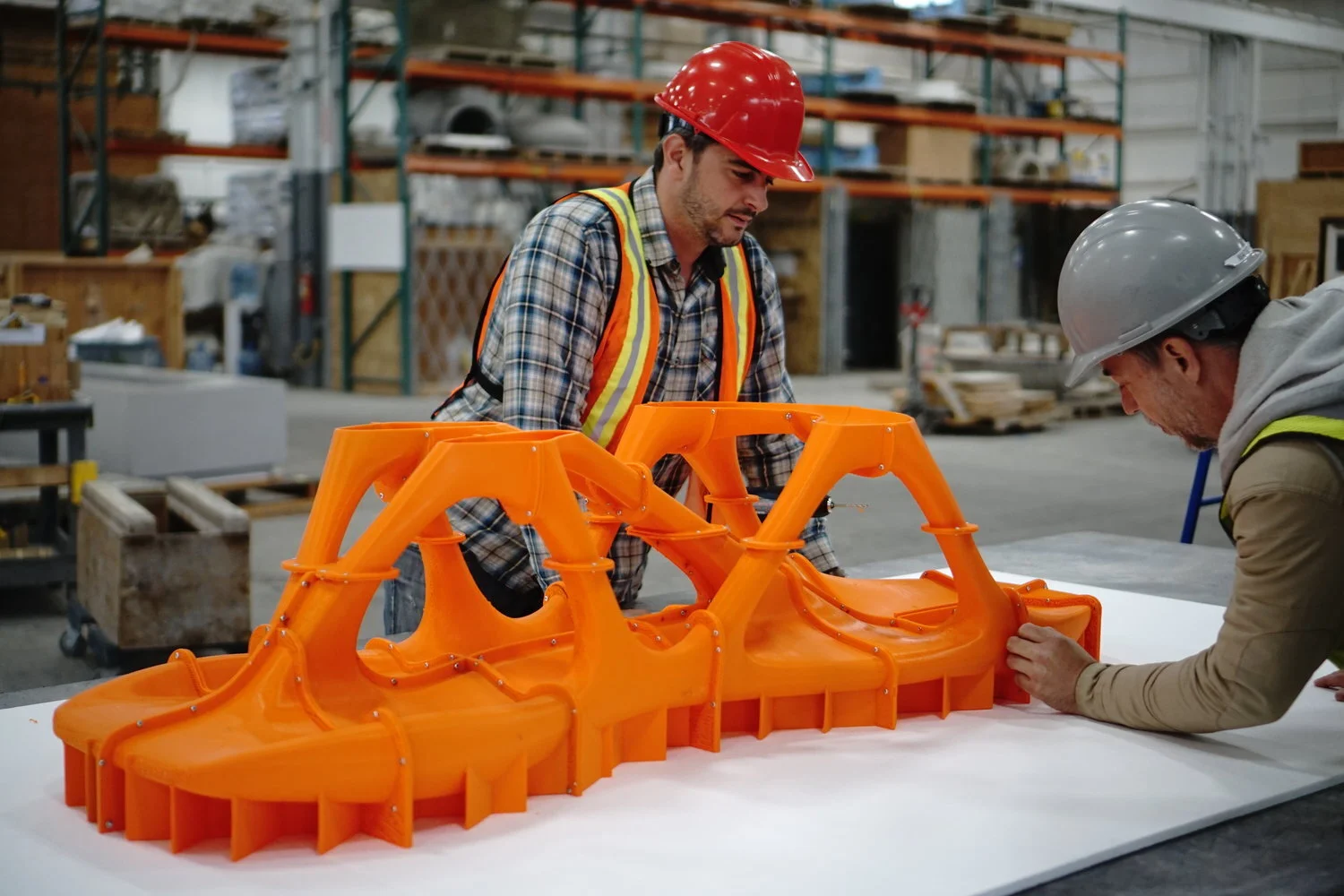

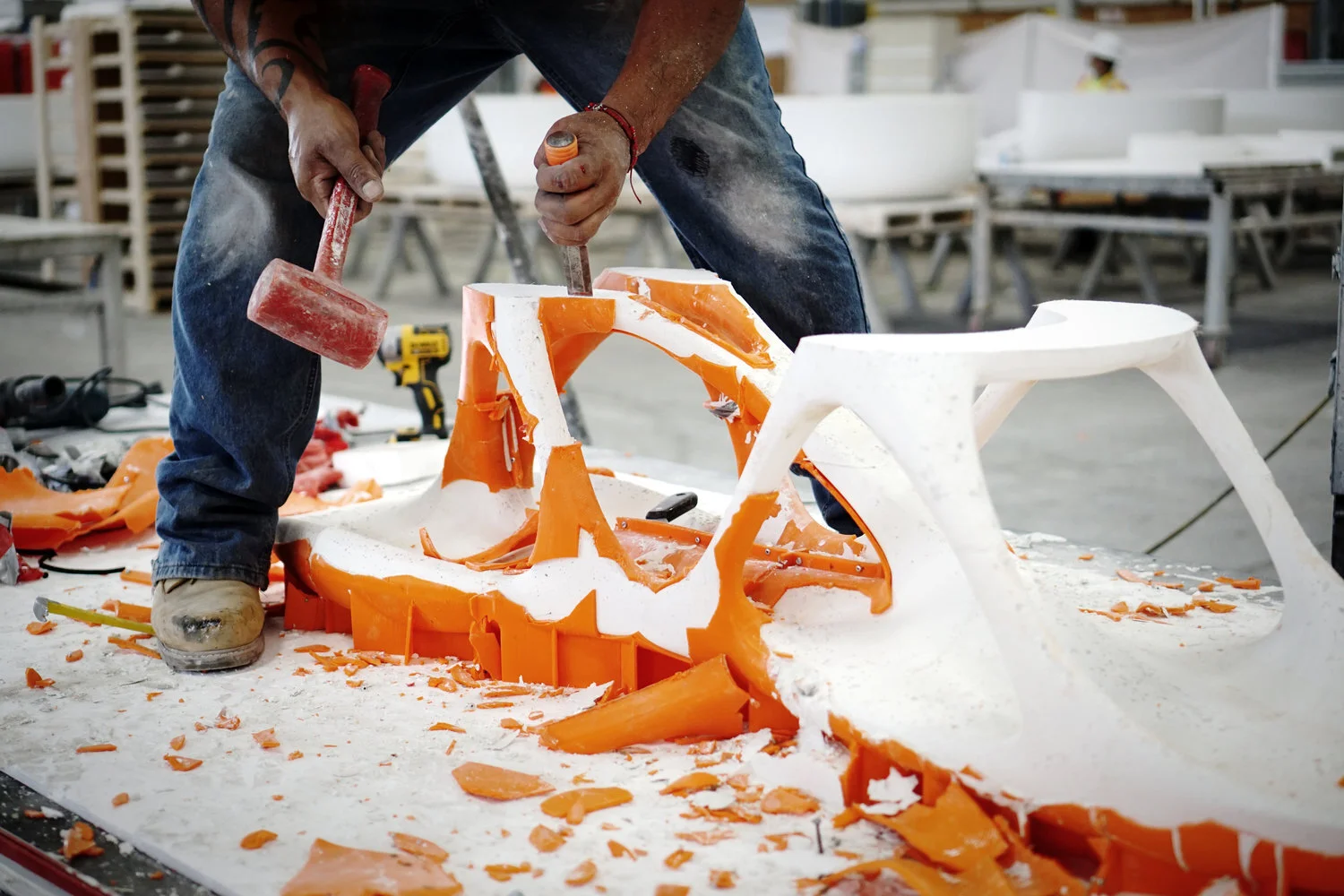
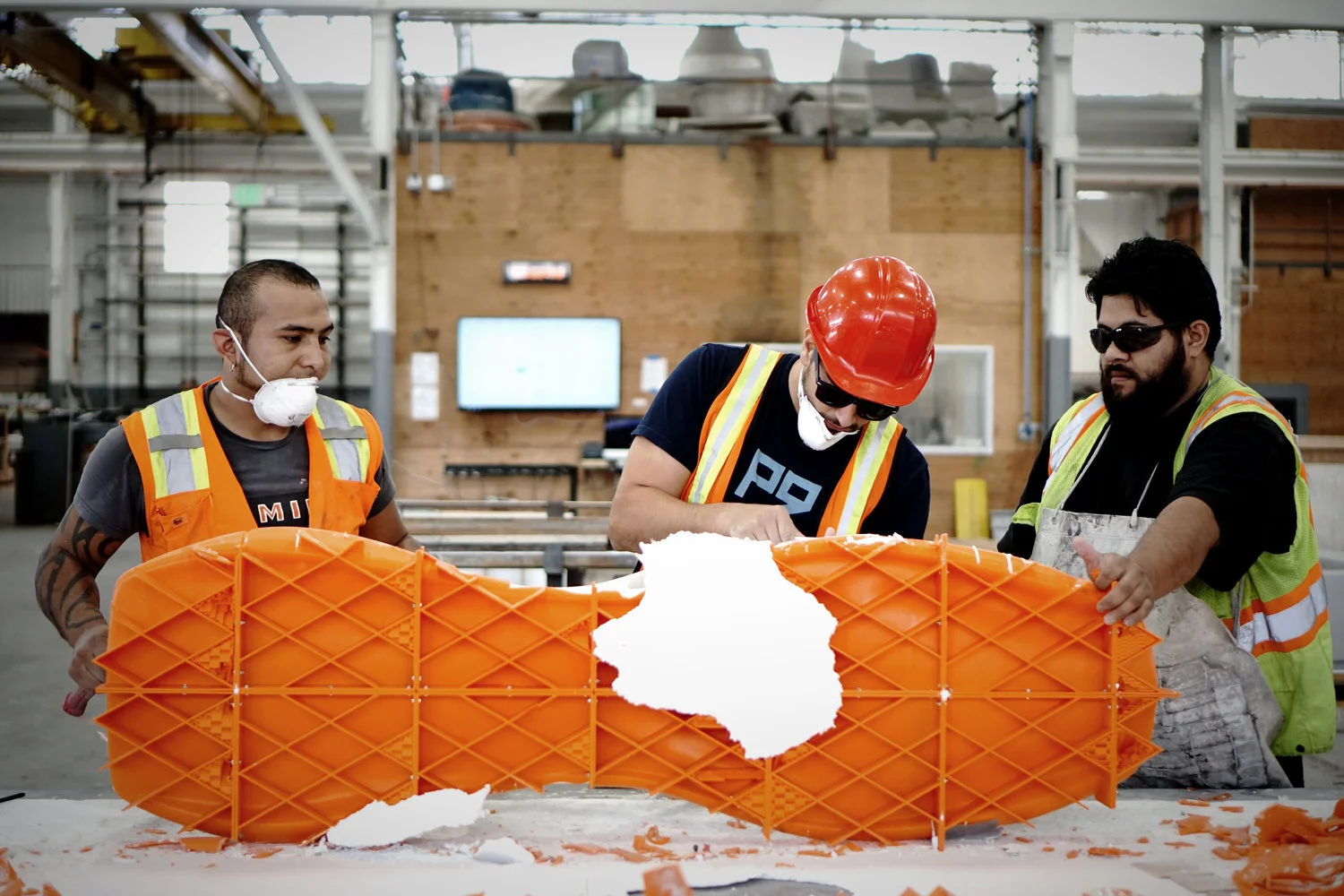

